Company History
Malcolm S. Anderson was born on a farm near New Harmony, Indiana, on May 21, 1910.
In the mid 1930’s he moved to South Bend, Indiana, to work in a chemical testing laboratory run by his older brother, Lural.
Because of the expertise he developed in his brother’s laboratory, “Mac” was offered a job as a metallurgist at a stainless steel foundry in Michigan City, Indiana.
In 1943 Mac was offered a job as a metallurgist in the laboratory at the C.G. Conn Company in Elkhart, Indiana, to troubleshoot some problems Conn was having with their wartime production.
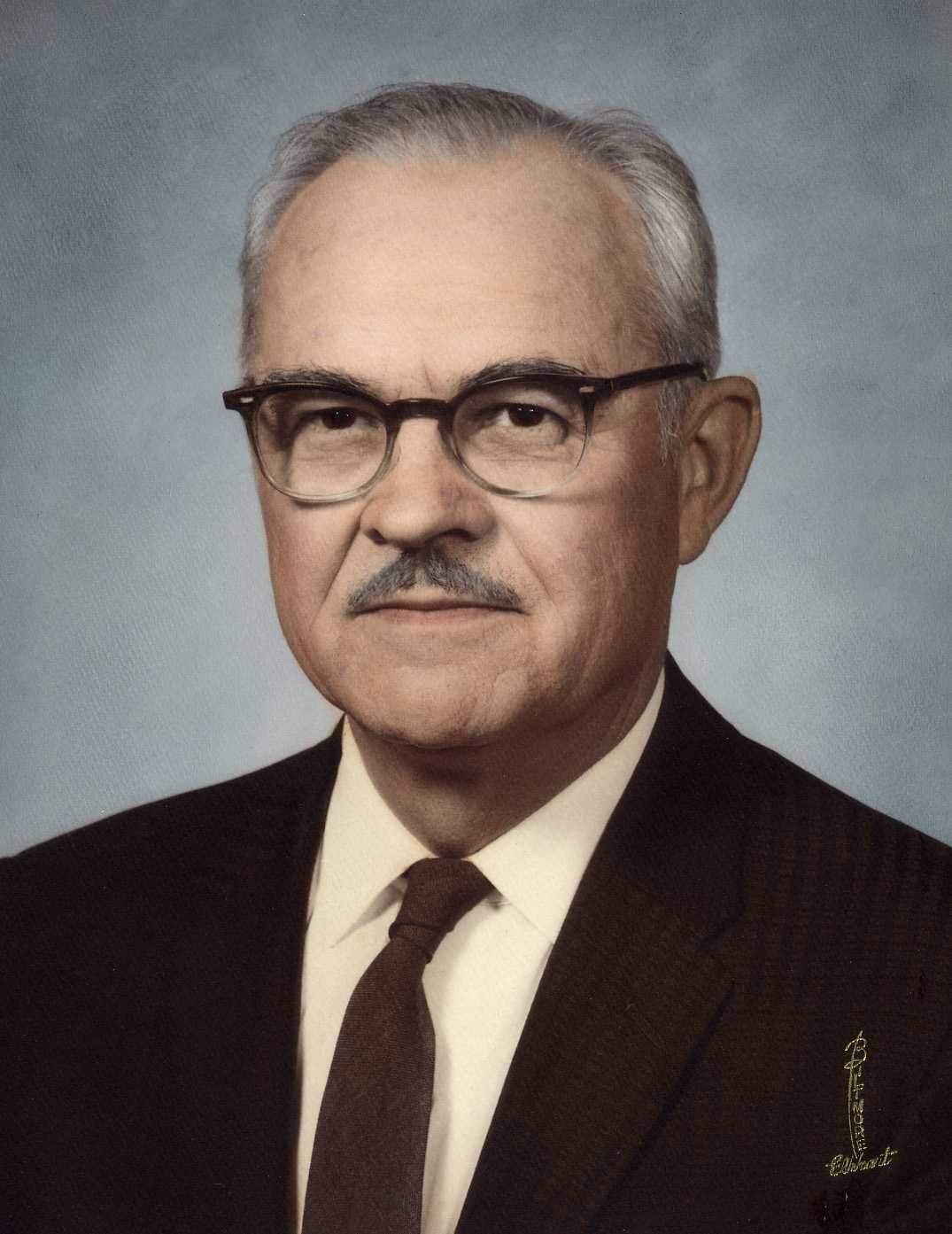
When the United States entered the second World War, the C.G. Conn Company was converted from manufacturing band instruments to producing hardware for the United State Military. Some of the products Conn provided were:
- Radar wave guide tubes
- Landing ship compass for the navy
- Altimeters for United States Aircraft
- Gyro-Horizons
- Bomb sights
- Tank tread link pins
- Main bearings for Allison aircraft engines
Mac worked long hours six or seven days a week with the laboratory and engineering staff to help Conn maintain excellent quality and meet delivery schedules. This job took him to all parts of the plant and made him familiar with all the facets of manufacturing. After a couple of years with Conn, Mac was made head of the entire laboratory.
When World War II ended, the C.G. Conn Company was able to go back to the business of being the world’s largest manufacturer of band instruments, and within a couple of years Mac was made superintendent of the entire plant. During his vacations, he worked as a metallurgical consultant for companies not competing with Conn.
The C.G. Conn Company was the only band instrument manufacturer in Elkhart to have its own plating line, a department Mac became very familiar with while maintaining the plating chemistry from the laboratory. The other band instrument manufacturers in Elkhart had to use an outside plating source that gave less than perfect results.
In 1948, Mac started Anderson Silver Plating, and his attention to detail and perseverance of quality allowed Anderson’s to be a plating source for aerospace and military specification plating, as well as electronics. His primary interest was always of being a service to the band instrument industry. His policy of plating anything from a piccolo key to a sousaphone with excellent quality and service at reasonable prices grew the company to become the largest independent plater of band instruments in the world.
The plating shop grew from a 1700 square foot building on South Main Street to the present 30,000 square foot facility on Industrial Parkway. At one time his company plated over 400,000 band instruments a year for a dozen and a half different manufacturers and 700 different dealers around the United States.
While Mac would always share his knowledge in production, metallurgy, and plating with his customers, he was always careful not to transfer information from one customer to another.
In 1975, at the age of 65, while maintaining an office and his position in the laboratory, Mac handed the operation of Anderson Silver Plating over to his son, Michael.
Mike started working summers at his father’s side in Anderson Silver Plating’s laboratory while in high school. After receiving his bachelor’s of science degree from Purdue University and commission from the U. S. Army, serving two years active duty as an officer, Mike started working on the floor and in the lab at Anderson Silver Plating Company.
Upon Mac’s retirement in 1975, Mike completed his ascension into the position of president at Anderson Silver Plating Company. Inc.